Items
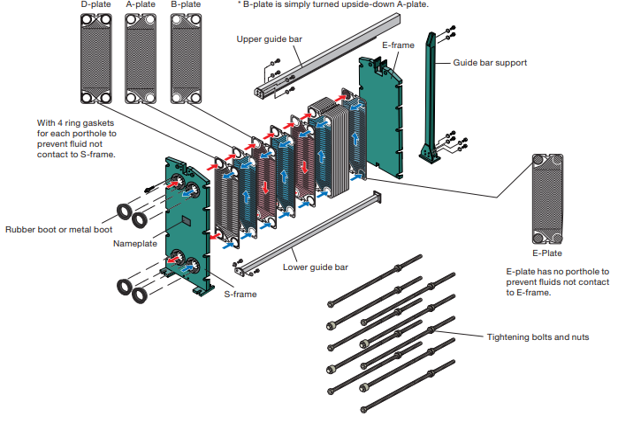
Plate Heat Exchanger
Abstract
Plate heat exchangers are composed of key components such as heat transfer plates, gaskets, frames, and tightening bolts. Among these, the heat transfer plates generate strong turbulence, resulting in high heat exchange performance, while the gaskets not only form the flow paths for the primary and secondary fluids but also serve the function of sealing.
Advantage
Application
01
Heat Transfer Plate Structure
The heat transfer plates can have various herringbone patterns, which increase strength and surface area. These patterns create high turbulence, improving heat transfer efficiency. The angle of the pattern is designed differently according to the physical properties and flow rate of the industrial fluid, thus adjusting the fluid passage rate and heat transfer effect. All heat transfer plates share the common feature of having four portholes and a seat for attaching gaskets that prevent fluid leakage to the outside.
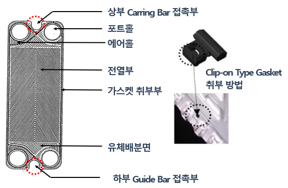
02
Flow Configuration
Plate Heat Exchanger (PHE) forms flow channels by stacking thin, corrugated heat transfer plates between a fixed frame and a moving frame. The formed flow channels allow more than two types of fluids to pass and exchange heat. The turbulence caused by the corrugation of the plates results in high heat transfer efficiency, making PHEs over five times more efficient than other types of heat exchangers (e.g., S&T, etc.). Fluids always form a counterflow configuration, which enables higher heat transfer efficiency.
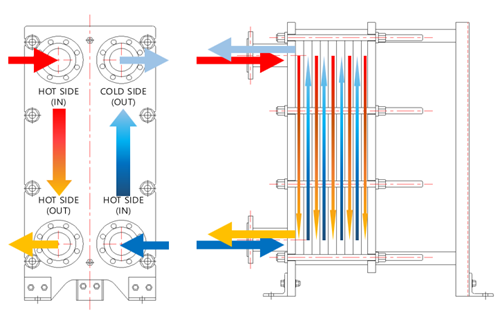
03
Single-Pass Structure
The single-pass structure is the most basic flow channel configuration of plate heat exchangers and is considered the most stable structure. Typically, the hot side is on the left and designed to flow from the top to the bottom, while the cold side is positioned on the right and flows from the bottom to the top, forming a counterflow that allows for designs with LMTD below 1℃. When high heat transfer efficiency is required, models with a longer vertical plate shape are selected, and when higher fluid throughput is required, models with a shorter vertical plate shape are selected, optimizing heat transfer efficiency and pressure drop characteristics to the process.
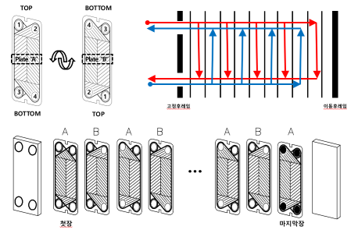
04
Multi-Pass Structure
Multi-pass structures are used in situations where there is a significant temperature change (ΔT) or low LMTD. When the flow rate of A/B sides is asymmetric, some flow channels are designed in a multi-pass configuration. Multi-pass structures provide good heat transfer efficiency due to the long fluid flow within the heat exchanger, but they are vulnerable to pressure drop. In the case of highly viscous fluids, external leaks can occur at the portholes of intermediate plates due to scale accumulation. Industries such as the food industry commonly use multi-pass configurations for sterilization purposes, and for maximum energy absorption in waste heat recovery.
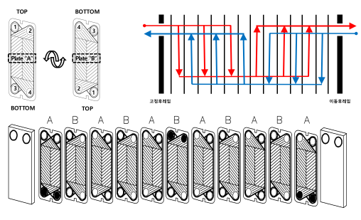
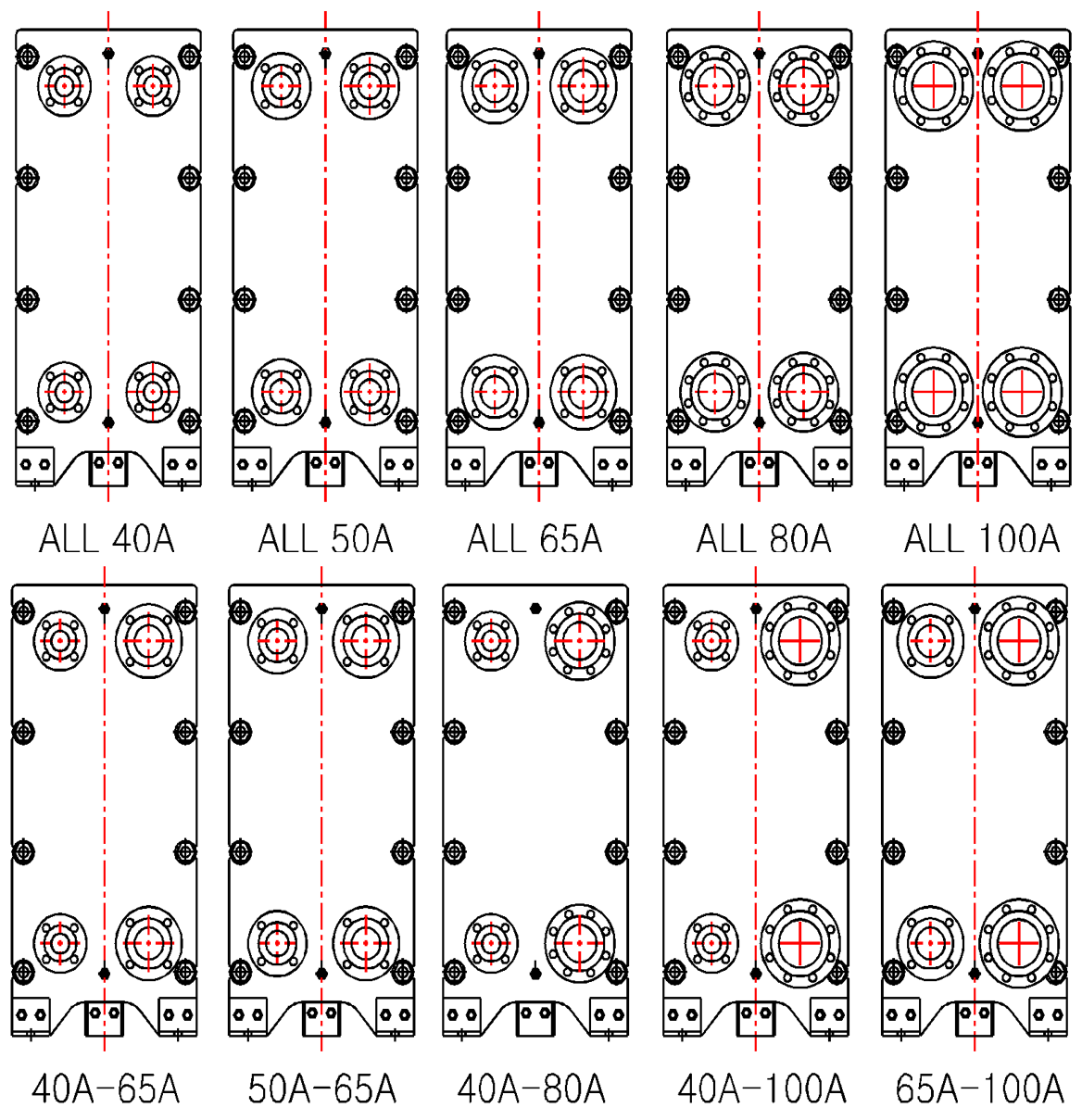
Custom P.H.Ex
SBHE selects nozzles to match the heat management system or product production process, which allows for minimizing the deviation between the target heat management temperature specified in the specification and the actual temperature control in the field process. By properly matching the physical properties and flow rate of the fluids moving through the piping, SBHE establishes a stable heat management system, eliminating the need for reducers or elbows, leading to a more stable system.
Furthermore, when there is a significant asymmetry in flow due to different temperature changes (ΔT) between the heating and heated media, SBHE can manufacture heat exchangers tailored to the pump and piping of the system. This system-integrated customization is advantageous for responding to events occurring during process operation or continuous work, and simplifies construction and maintenance, thus reducing CAPEX/OPEX.
Vapor Design
SBHE extensively utilizes heat exchangers in various industries where vapor is used as a heat source, including saturated steam, dry saturated steam, and superheated steam. SBHE is capable of applying steam in all areas to meet customer requirements and providing perfect solutions.
Since vapor transfers heat by changing state from steam to condensate and utilizing latent heat, SBHE accurately calculates the steam supply rate (Velocity) and steam passage rate entering the heat exchanger according to the customer’s process. The appropriate nozzle size is selected for draining the condensate, which prevents events such as water hammering.
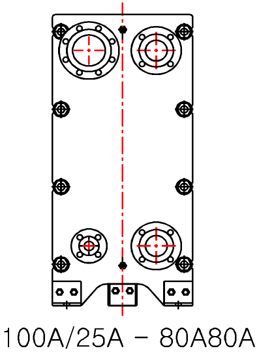

Variety Models
SBHE strives to provide customers with customized heat exchangers by launching various models, aiming to offer higher efficiency and utility. To achieve this, we focus on manufacturing heat exchangers integrated into systems for all industrial processes, dedicating ourselves to developing related technologies and products, and constantly improving our services.
We thoroughly review all details to deliver the optimal performance at the precise target temperature, swiftly and accurately to our customers.